A comprehensive Overview of 3D Printing echnologies
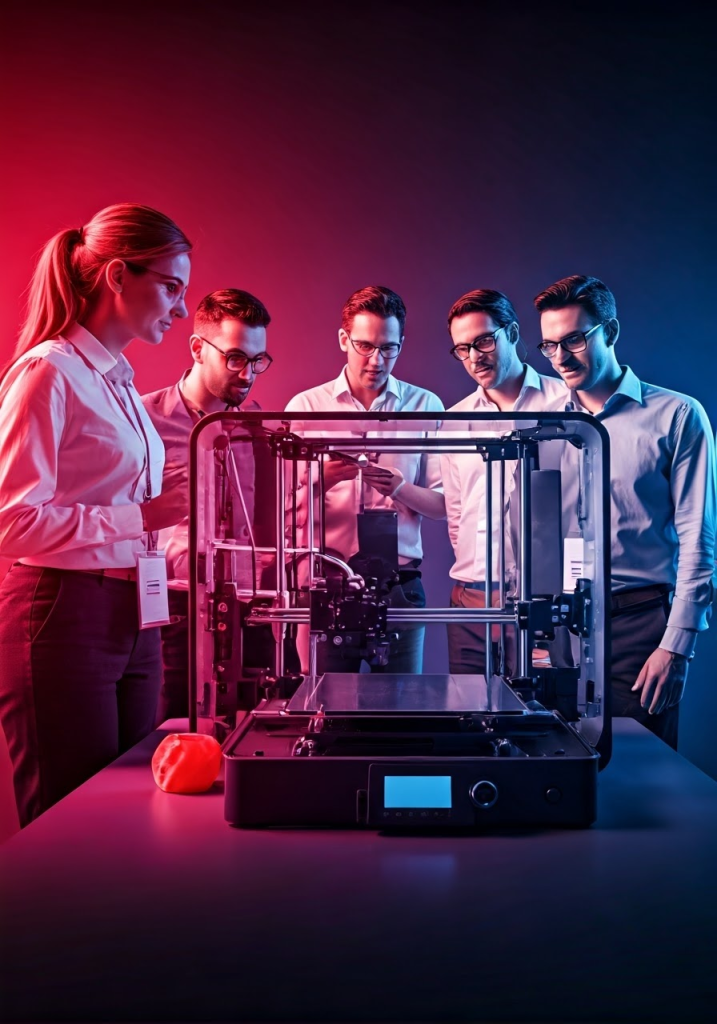
Explore 3D through Essential Educational Resources
If you’re new to 3D printing, welcome aboard! You’re in for an exciting journey that’s not only fun and inspiring but also incredibly practical and potentially profitable.
For those new to 3D printing, understanding the diverse methods involved can be quite challenging. While many envision 3D printing as simply layering plastic filaments to create objects, it’s actually a broad field that covers various processes, each with its unique machines and materials. Referred to as additive manufacturing, 3D printing is capable of producing a wide range of items, from simple pencil holders to complex rocket engines.
What all these processes share is their digital foundation. Every 3D printed object begins as a digital model, usually created with computer-aided design (CAD) software or sourced from a digital repository. This model is then processed through specialized software that slices it into layers, creating a set of instructions for the 3D printer to follow. These instructions, specific to the type of 3D printer and even the brand, guide the machine in building the object layer by layer.
This guide will walk you through the different 3D printing technologies, explaining what each one is typically used for. Additionally, we’ll link to more in-depth articles that list the best 3D printers for each technology type.
The International Standards Organization (ISO) classifies additive manufacturing into seven general types, providing a structured understanding of the technology globally. These types could be divided by the final product they create or the materials they use, but ISO’s classification helps in organizing the wide-ranging applications of 3D printing.
By understanding these distinctions, you’ll gain a clearer picture of how versatile and powerful 3D printing technology truly is.
Material extrusion
Material extrusion, often abbreviated as MEX, is a 3D printing process where material is pushed through a heated nozzle, nearly melting it in the process. The material is then deposited layer by layer on a build platform, following a path defined by digital build preparation software. As the material cools, it solidifies to form a solid object. This method is most commonly associated with plastics, but the range of materials that can be used is vast, including metal pastes, concrete, biogels, and even food.
Despite its apparent simplicity, material extrusion is an incredibly versatile process. The diversity of materials that can be extruded means that this method can be adapted to a wide range of applications, from creating small prototypes and complex components to printing entire structures like houses. The costs of 3D printers that use material extrusion vary widely, from affordable models priced around $100 to highly sophisticated machines that can cost up to seven figures.
The subtypes of material extrusion include Fused Deposition Modeling (FDM), which is the most common and widely recognized form, construction 3D printing for building large-scale structures, micro 3D printing for intricate details, bio 3D printing for medical and biological applications, and Fused Granulate Modeling (FGM), which allows for the use of more granular materials.
Material extrusion’s versatility extends to its applications. It’s commonly used for creating prototypes, electrical housings, jigs and fixtures, and even investment casting patterns. However, it is also being utilized in innovative ways, such as in the construction industry for building houses, and in the medical field for printing biocompatible structures.
While material extrusion is the most cost-effective 3D printing method and supports a broad spectrum of materials, it does have some limitations. The printed objects may not always possess the same strength, durability, or dimensional accuracy as those produced by other 3D printing techniques. The method’s dimensional accuracy is typically within ±0.5%, with a lower limit of ±0.5 mm. Despite these challenges, the method’s affordability and material flexibility make it a popular choice across various industries.
Fused Deposition Modeling (FDM)
Fused Deposition Modeling (FDM) is a cornerstone of the 3D printing industry, ranging from simple models for hobbyists to advanced machines for industrial use. Often known as Fused Filament Fabrication (FFF), this technique primarily involves extruding plastic filament through a heated nozzle, layering it to form objects. A variant, Fused Granulate Modeling (FGM), uses polymer pellets instead of filament, which can be more cost-effective and is frequently used in professional settings. FDM technology can also handle a variety of materials, including ceramics, metals, and even food.
The process begins with a digital model, which is translated into instructions for the 3D printer. For filament-based FDM printers, plastic filament is loaded and fed through the printer’s nozzle, which heats the material to a point where it softens and can be extruded layer by layer. The print head moves along the X and Y axes to deposit the material, while the bed or the print head itself adjusts along the Z axis to build up layers and create the final object.
3D bioprinting
At 3D IT, we are pioneering advancements in 3D bioprinting, a cutting-edge additive manufacturing process that blends living cells and biological materials to create three-dimensional tissue-like structures. This technology goes beyond traditional 3D printing by allowing the creation of complex, organic forms such as bone tissue, blood vessels, and even entire living tissues. Bioprinting has transformative potential in medical research, from tissue engineering and drug development to regenerative medicine therapies.
3D bioprinting shares similarities with traditional Fused Deposition Modeling (FDM) but uses specialized materials called bioinks. These bioinks are primarily composed of living cells embedded in a carrier material like collagen, gelatin, or alginate, which provides the necessary support and nutrients for the cells to thrive and form functional tissue. The bioink is extruded through a needle or nozzle, layer by layer, to build structures that closely mimic natural tissues.
As the technology evolves, 3D bioprinting is expanding its reach into various fields, including the production of cultured meat, where bioinks are used to print cell-based meat products. This process holds the promise of revolutionizing the way we approach not only medicine but also sustainable food production.
At 3D IT, we are committed to exploring and harnessing the full potential of 3D bioprinting, driving innovation in fields that impact both human health and the future of our food systems. By integrating this advanced technology into our operations, we are at the forefront of a revolution in how we understand and apply 3D printing in biological and medical sciences.
The process begins with a digital model, which is translated into instructions for the 3D printer. For filament-based FDM printers, plastic filament is loaded and fed through the printer’s nozzle, which heats the material to a point where it softens and can be extruded layer by layer. The print head moves along the X and Y axes to deposit the material, while the bed or the print head itself adjusts along the Z axis to build up layers and create the final object.
In cases where polymer pellets are used instead of filament, the process is similar. The pellets are fed from a hopper into the extruder, melted, and then extruded in the same manner as filament. The versatility of FDM extends to the types of materials it can process. While plastic is the most common material, FDM has been adapted to work with a wide variety of other substances, including ceramics, glass, clay, chocolate, and even metals.
Metal FDM is particularly noteworthy as it involves using a plastic filament filled with metal powder, typically more than 80% metal by volume. This process allows for the production of metal parts, although several post-processing steps are required to achieve the final product.
Depending on the complexity of the object being printed, support structures may be needed to prevent overhangs or other challenging geometries from collapsing during the printing process. These supports are typically made from a dissolvable material, making them easier to remove after printing.
Overall, FDM is favored for its affordability and the broad range of materials it can accommodate, making it suitable for applications from simple prototypes to complex, functional parts in various industries.
Despite its apparent simplicity, material extrusion is an incredibly versatile process. The diversity of materials that can be extruded means that this method can be adapted to a wide range of applications, from creating small prototypes and complex components to printing entire structures like houses. The costs of 3D printers that use material extrusion vary widely, from affordable models priced around $100 to highly sophisticated machines that can cost up to seven figures.
The subtypes of material extrusion include Fused Deposition Modeling (FDM), which is the most common and widely recognized form, construction 3D printing for building large-scale structures, micro 3D printing for intricate details, bio 3D printing for medical and biological applications, and Fused Granulate Modeling (FGM), which allows for the use of more granular materials.
Material extrusion’s versatility extends to its applications. It’s commonly used for creating prototypes, electrical housings, jigs and fixtures, and even investment casting patterns. However, it is also being utilized in innovative ways, such as in the construction industry for building houses, and in the medical field for printing biocompatible structures.
While material extrusion is the most cost-effective 3D printing method and supports a broad spectrum of materials, it does have some limitations. The printed objects may not always possess the same strength, durability, or dimensional accuracy as those produced by other 3D printing techniques. The method’s dimensional accuracy is typically within ±0.5%, with a lower limit of ±0.5 mm. Despite these challenges, the method’s affordability and material flexibility make it a popular choice across various industries.
Construction 3D printing
Construction 3D printing is revolutionizing the building industry, leveraging massive 3D printers that extrude materials like concrete to create structures directly on-site. These printers, which can be as tall as several stories, use either gantry or robotic arm systems to build everything from homes to complex infrastructure projects. This technology is not only cutting down on labor costs and construction waste but is also pushing the boundaries of sustainable building practices.
At 3D IT, we recognize the transformative potential of this technology. By integrating local materials into the construction process, such as using soil instead of concrete, construction 3D printing can significantly reduce the environmental impact of building projects. This method aligns with our commitment to sustainable innovation.
**Example:** Consider the ongoing research into building habitats on the moon and Mars using 3D printing technology. These efforts aim to use in-situ materials, like lunar or Martian soil, to construct shelters for future space missions. This approach not only demonstrates the versatility of construction 3D printing but also its potential to make human habitation on other planets feasible.
In addition to extraterrestrial construction, this technology is already being applied on Earth, with hundreds of 3D-printed homes built worldwide. These structures showcase the efficiency and sustainability that 3D printing brings to the construction industry. By reducing the need for manual labor and minimizing waste, construction 3D printing offers a glimpse into the future of how we might build not only homes but entire communities, whether on Earth or beyond.
3D bioprinting shares similarities with traditional Fused Deposition Modeling (FDM) but uses specialized materials called bioinks. These bioinks are primarily composed of living cells embedded in a carrier material like collagen, gelatin, or alginate, which provides the necessary support and nutrients for the cells to thrive and form functional tissue. The bioink is extruded through a needle or nozzle, layer by layer, to build structures that closely mimic natural tissues.
As the technology evolves, 3D bioprinting is expanding its reach into various fields, including the production of cultured meat, where bioinks are used to print cell-based meat products. This process holds the promise of revolutionizing the way we approach not only medicine but also sustainable food production.
At 3D IT, we are committed to exploring and harnessing the full potential of 3D bioprinting, driving innovation in fields that impact both human health and the future of our food systems. By integrating this advanced technology into our operations, we are at the forefront of a revolution in how we understand and apply 3D printing in biological and medical sciences.
The process begins with a digital model, which is translated into instructions for the 3D printer. For filament-based FDM printers, plastic filament is loaded and fed through the printer’s nozzle, which heats the material to a point where it softens and can be extruded layer by layer. The print head moves along the X and Y axes to deposit the material, while the bed or the print head itself adjusts along the Z axis to build up layers and create the final object.
Vat Polymerization (RESIN 3D)
Vat polymerization, often referred to as resin 3D printing, represents a cutting-edge segment of additive manufacturing that 3D IT leverages to deliver products with exceptional detail and precision. This technology operates by curing layers of photopolymer resin using a focused light source, which hardens the liquid material into solid forms as per the digital design. The ability to precisely direct light onto specific areas of the resin allows for the creation of intricate details and smooth surfaces, making this process ideal for applications requiring high accuracy.
At 3D IT, we utilize various types of vat polymerization technologies, each suited for specific applications:
Stereolithography (SLA): SLA is one of the most well-known forms of vat polymerization, using a laser to trace and harden each layer of the resin. It’s particularly effective for creating detailed prototypes, jewelry casting models, and dental applications. The resulting parts have smooth surfaces and fine feature details, which are crucial for products where precision is paramount.
Digital Light Processing (DLP): DLP technology uses a digital projector to flash a single image of each layer onto the resin surface, curing it all at once. This method is faster than SLA and is ideal for creating larger parts without compromising detail and accuracy. DLP’s ability to produce high-resolution parts quickly makes it a popular choice for consumer product prototyping and small-scale production.
Liquid Crystal Display (LCD): Also known as Masked Stereolithography (MSLA), LCD technology uses an array of LEDs shining through an LCD screen that masks the areas not being cured. This method is similar to DLP but can be more cost-effective, making it accessible for various applications from hobbyist projects to professional-grade prototypes.
Innovative Variants: Beyond these traditional methods, there are unique technologies developed by specific manufacturers. For example, Carbon’s Digital Light Synthesis (DLS) and Formlabs’ Low Force Stereolithography (LFS) are proprietary technologies that push the boundaries of vat polymerization, offering improved mechanical properties, faster print times, and the ability to work with more complex materials.
Example Application: An excellent example of vat polymerization’s capabilities is in the field of dentistry, where custom dental aligners are produced using SLA. These aligners require an exact fit, which is achieved through the high precision of vat polymerization. The digital model of a patient’s teeth is used to create a series of aligners that gradually adjust the alignment of the teeth, providing both effectiveness and comfort.
Materials and Post-Processing: The materials used in vat polymerization are known as photopolymer resins, which can vary widely depending on the application. These include castable resins for jewelry, biocompatible resins for medical uses, and even resins filled with metal or ceramic particles for enhanced properties. After printing, the parts often require cleaning to remove uncured resin, followed by additional curing in a UV chamber or under sunlight to fully solidify and strengthen the material. This post-processing is essential to ensure the final product meets the desired mechanical and aesthetic properties.
At 3D IT, we understand that each project has unique requirements, and our vat polymerization services are tailored to meet those needs. Whether producing prototypes that mimic the qualities of injection-molded parts or creating final-use components with complex geometries, our advanced vat polymerization technologies ensure that we deliver parts with the highest level of detail, precision, and quality.
Stereolithog-raphy (SLA)
Stereolithography (SLA) holds a special place in the history of 3D printing, being the first technology of its kind. Invented by Chuck Hull in 1986, who later founded 3D Systems to bring it to market, SLA has since evolved into a widely used technology by both hobbyists and professionals. At 3D IT, we harness the precision and versatility of SLA to deliver high-quality 3D prints with exceptional detail and smooth surfaces, ideal for complex prototypes and intricate designs.
SLA technology operates by directing a laser beam across a vat of liquid resin, using mirrors known as galvanometers to precisely aim the laser. This laser selectively cures and solidifies each layer of the object, building it up one layer at a time. The build platform then moves slightly to make room for the next layer, which is cured in the same manner.
While SLA may take longer to complete each layer compared to other methods like Digital Light Processing (DLP), it offers unique advantages. The laser used in SLA printers can generate a stronger light, which is necessary for curing engineering-grade resins that require higher energy to solidify properly. This makes SLA particularly well-suited for applications that demand high strength and durability in the final product.
Example Application: SLA technology is widely used in the production of dental models, where precision and accuracy are paramount. For instance, custom dental aligners are often created using SLA printers to ensure a perfect fit for each patient. The detailed layer-by-layer curing process allows for the production of highly accurate models, which are then used to form the aligners that gradually adjust the patient’s teeth.
At 3D IT, we utilize SLA technology to produce parts with superior surface finishes and intricate details. Whether for creating prototypes, end-use parts, or highly detailed models, our SLA services ensure that each project meets the highest standards of quality and precision. This makes SLA a vital component of our comprehensive 3D printing offerings, enabling us to cater to a wide range of industries and applications.
Microstereol-ithography
Microstereolithography (µSLA) is an advanced variation of stereolithography within the vat polymerization family, designed for creating parts on a micro-scale with incredibly high resolution, ranging from 2 microns to 50 microns. To put this into perspective, the width of a human hair is about 75 microns. This technology is part of what is often referred to as “micro 3D printing.”
At 3D IT, we employ µSLA to achieve unparalleled precision in producing miniature components, which are crucial for industries such as medical devices, microelectronics, and advanced manufacturing. The µSLA process involves using highly specialized resins and sophisticated ultraviolet lasers, combined with precision lenses, to focus light on extremely small points. This allows for the creation of detailed microstructures that would be impossible to achieve with traditional 3D printing technologies.
Example Application: Consider the production of microfluidic devices, which are essential in medical diagnostics and drug delivery systems. µSLA technology allows us to manufacture these devices with the precise channels and features required for their functionality. The ability to produce such intricate components at a micro-scale is what makes µSLA invaluable in fields where precision is non-negotiable.
At 3D IT, our use of µSLA enables us to push the boundaries of what’s possible in 3D printing, delivering solutions that meet the most demanding requirements for accuracy and detail. Whether it’s for scientific research, advanced manufacturing, or specialized medical applications, µSLA is a key technology in our arsenal, allowing us to offer cutting-edge micro-scale 3D printing services to our clients.
Two-Photon Polymerization (TPP)
Two-Photon Polymerization (TPP), also known as 2PP, is a highly specialized micro 3D printing technology that takes precision to the next level, enabling the creation of parts as small as 0.1 microns. Categorized under SLA due to its use of a laser and photosensitive resin, TPP involves a pulsed femtosecond laser that focuses on a specific point in a vat of special resin. This tight spot cures individual 3D pixels, known as voxels, which are then sequentially layered to form a complete 3D object. The objects produced can be several millimeters in size while maintaining nanometer resolution.
At 3D IT, we utilize TPP for applications that require extreme precision and detail, such as in advanced research, medical devices, and manufacturing of tiny components like micro-sized electrodes and optical sensors. The ability to produce such minute and intricate structures opens up possibilities for innovations in fields that demand the highest level of accuracy.
Example Application: In the medical field, TPP is used to create micro-sized optical sensors that can be integrated into advanced diagnostic equipment. These sensors require nanometer-scale precision to function correctly, and TPP’s ability to produce such detailed parts makes it an invaluable technology in the development of next-generation medical devices.
By incorporating TPP into our suite of 3D printing services, 3D IT continues to push the boundaries of what is possible in additive manufacturing, offering solutions that meet the most exacting standards of precision and detail. This technology is essential for clients who require components that operate at the micro and nanoscale, ensuring that their projects benefit from the highest levels of innovation and quality.
Digital Light Processing (DLP)
At 3D IT, we harness Digital Light Processing (DLP) technology to efficiently produce larger parts or multiple items in a single batch. DLP’s advantage lies in its ability to project an entire layer of a 3D model at once, making it faster than laser-based methods like SLA. The technology uses a digital micromirror device (DMD) to direct LED or UV light onto resin, curing layers in a matter of seconds.
DLP technology excels in delivering high-resolution prints, ideal for detailed and intricate designs. Modern DLP projectors, equipped with thousands of micrometer-sized LEDs, provide enhanced precision by individually controlling each light source. This allows 3D IT to produce accurate and finely detailed parts at a much quicker rate, making DLP particularly suited for applications that require both speed and precision, such as dental prosthetics and intricate consumer products.
Example Application:In the field of dentistry, 3D IT leverages DLP technology to produce dental prosthetics rapidly and with high accuracy. By projecting each layer in one go, DLP enables the fast production of multiple high-resolution parts, such as dental crowns and models, which are essential for timely patient care.
Not all DLP machines are created equal, with significant differences in the quality of the light source, lenses, and DMD. This variation can lead to machines ranging in price from $300 to over $200,000. At 3D IT, we invest in top-tier DLP printers, ensuring that every project meets the highest standards of quality, regardless of its complexity or scale.
UPSIDE DOWN DLP
Some DLP 3D printers are designed with the light source positioned at the top, directing light downward onto the resin vat. These “top-down” printers cure each layer from above, with the build plate lowering the solidified layer back into the vat. After each layer is cured, a recoater levels the resin for the next layer. This method offers greater stability for larger prints by working with gravity, reducing the stress on the build plate and minimizing the need for support structures, which the resin vat helps to maintain during printing.
At 3D IT, we are relentlessly pursuing the latest advancements in 3D printing technology to stay at the forefront of innovation. Our commitment to adopting and integrating cutting-edge techniques ensures that we continue to offer the most advanced solutions for your projects. As the 3D printing landscape evolves, we will keep you informed about important updates, emerging trends, and new developments in the field. We invite you to join us on this journey of discovery. For any inquiries or further discussion, please reach out to us at [mail@3dit.ai]. We’re always here to help you navigate the exciting world of 3D printing.
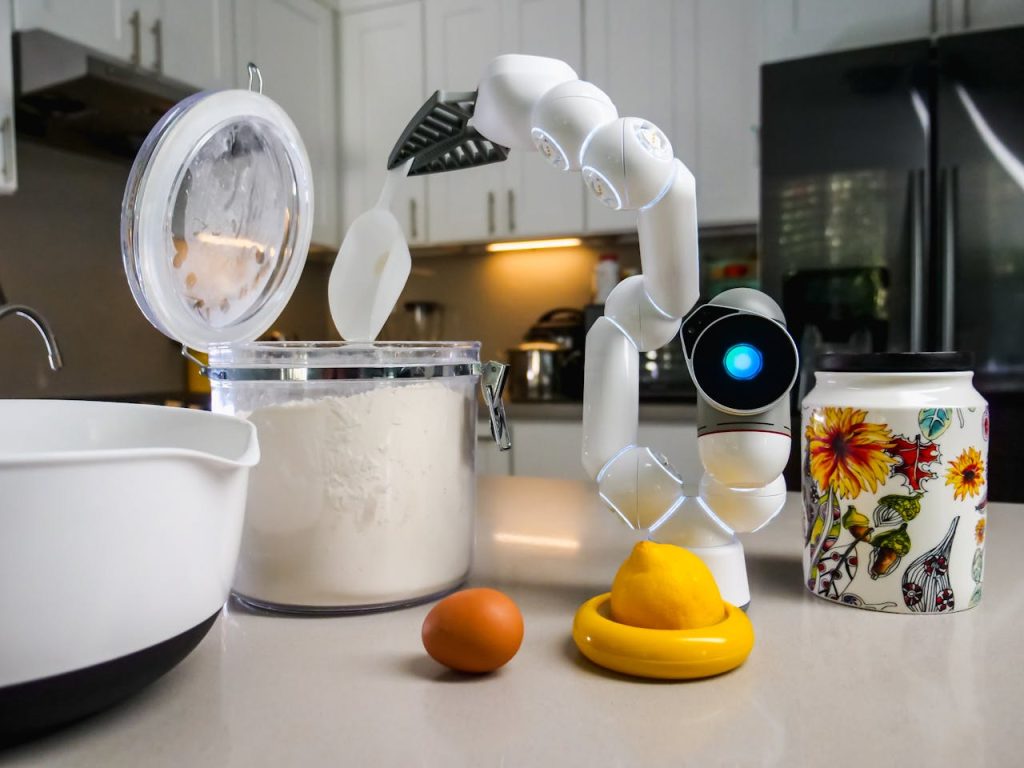